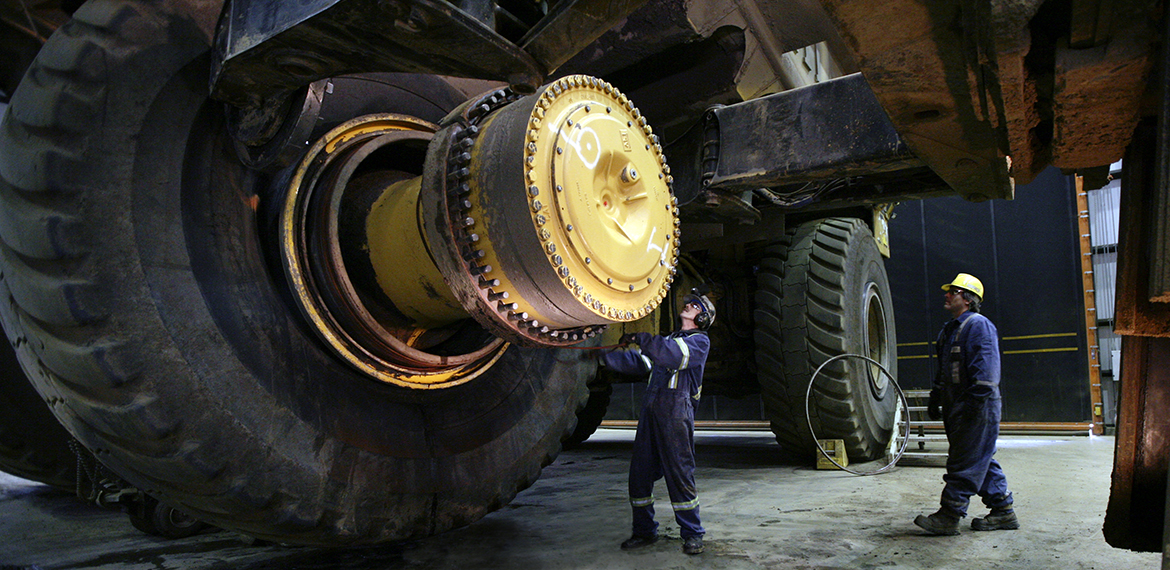
IT EXISTS in various forms in about 10 million different compounds and is one of the most abundant elements in the universe by mass.
Carbon is everywhere—in the form of fibre, charcoal, synthetic polymers, medical products, textiles, leather, printing inks, purification systems and the hardest known material, diamonds.
Carbon makes up 30 per cent or more of tire composition. That’s an important factor in the mining industry, which uses some of the largest machinery and transport trucks on the planet to move heavy materials through harsh terrain. The tires on the industry’s largest trucks can be as tall as 4 metres (13 feet) and weigh nearly 5,445 kg (12,000 lbs). They are made of durable materials and cost upwards of $50,000 each.
“The work we do with the Kal Tire Mining Tire Group and others allows us to embed our students and researchers into industry so they are job-ready.”
With that cost, there is little wonder that the industry is continuously searching for better ways to effectively and environmentally repurpose used mining tires. Due to the technological challenges, mines and their tire suppliers have stored used scrap tires for years.
Kal Tire Mining Tire Group recently developed a new process where mining tires can be recycled and broken down to a synthetic diesel fuel (for example, to power generators), steel products and carbon residue.
Enter UBC Okanagan’s School of Engineering, Associate Professor Lukas Bichler’s research team, and the The Spark Plasma Sintering (SPS) Research Laboratory.
The SPS is one of the only university labs in western Canada capable of preparing novel materials—ceramic, metallic, polymer, nano, bio, conductive, insulative and functionally graded materials and composites using the advanced SPS technique.
The particle fusion equipment compacts solid mass from powder through rapid heat generation and pressure. The technology is only one of the few capable to fabricate nanostructured materials, which are seen as next-generation materials.
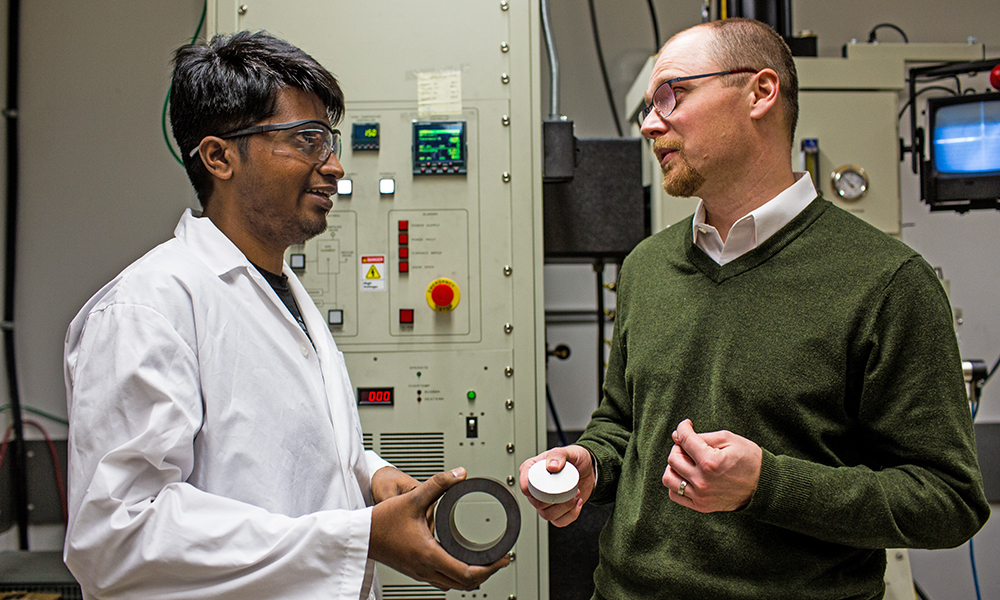
Lukas Bichler, right, in the SPS lab with his PhD student Anil Prasad.
How to ‘BEAR’ Results with Industry Partners
Bichler is a materials engineer specializing in material development, fabrication and part manufacturing. He and his team are collaborating with Kal Tire Mining Tire Group to upgrade the recycled carbon residue to make it usable for new applications.
“Carbon has a number of applications,” Bichler says. “It can be used in paints, filters, thermo-insulators, tires and batteries.”
The challenge in upgrading the recycled carbon for these applications is finding the right composition and structure of carbon that will work for a given system. For example, mining tires are contaminated on job sites, and these contaminants can carry through the recycling process.
“We have established excellent international partnerships to rapidly develop this technology.”
While Bichler jokes that he would happily keep the contaminants from diamond mines, he and his team are hard at work cleaning the carbon from coal and metal mines to provide a pure carbon. By developing processes that result in a purer carbon, the researchers are able to explore greater options for re-use.
Bichler’s team is also investigating how effectively the carbon can be used in the next generation of batteries. “The battery approach is just one in a long list of possible solutions we plan on investigating,” he says. “We have established excellent international partnerships to rapidly develop this technology.”
This is the first industry research partnership with the School of Engineering as part of the school’s new Boosting Engineering Applied Research (BEAR) Fund.
“The idea behind BEAR is that it is different from just building only the project-based research, it is more about the program—how we build a program in which industry partners, which could be local, regional, or international, can work closely with engineering researchers at UBC’s Okanagan campus,” says Prof. Rehan Sadiq, Associate Dean of the School of Engineering.
“The benefits are two-fold for our faculty to do cutting-edge research and applied research. At the same time, our industry partners will find a competitive edge and they will find a place in the market place.”
Innovation Centres Near and Far
Bichler is seizing the opportunity to partner with an international player.
“Kal Tire Mining Tire Group has given us a phenomenal level of support and access to their innovation centre in Vernon, BC, as well as their design team who are constructing a full-size recycling plant in Chile. We are working beyond the lab-scale and sharing our results with our partner so they can incorporate our findings into their processes.”
With nearly 80 per cent of engineers with PhDs working in industry, Bichler sees partnerships like this one as paramount to his lab’s success, and to student experience.
“The work we do with the Kal Tire Mining Tire Group and others allows us to embed our students and researchers into industry so they are job-ready.”
“We are going to be working together, trying to develop better materials that out-perform the existing benchmarks, and also materials which are cheaper to manufacture and easier to manufacture. This is an incredible opportunity for us both. And here we have a chance to open up and even show what we can do as a partner for other companies as well.”
Read more about Assoc. Prof. Lukas Bichler in UBC’s One Great Idea series.
Bichler describes the one great idea that significantly influenced his specific discipline and in turn, transformed how he approaches his work.