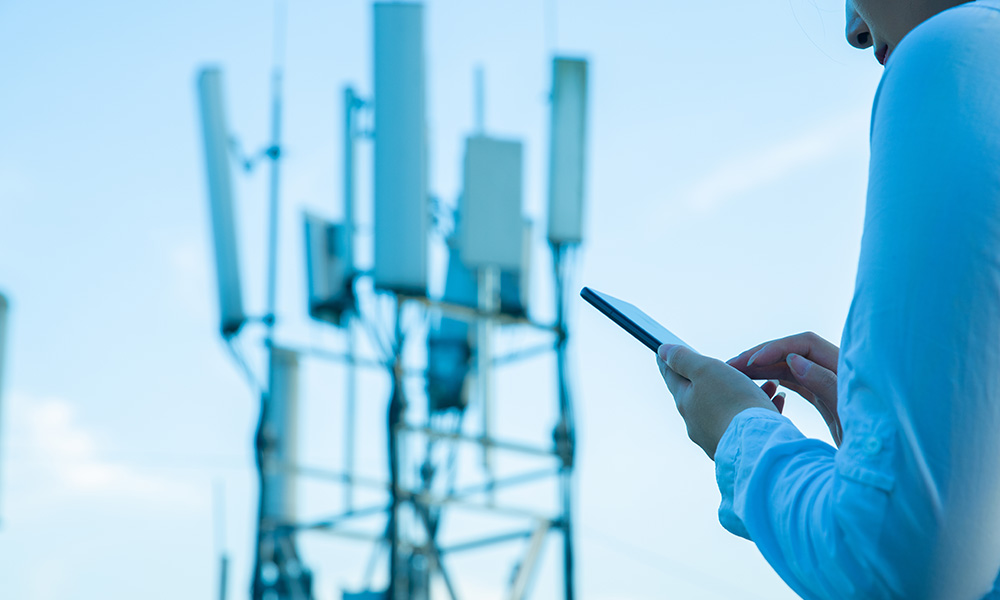
UBCO and Drexel University researchers have developed state-of-the-art communication components that have a compatible performance to metal, but are 10 to 20 times lighter, less expensive and easy to build.
In a first-of-its-kind development, UBC Okanagan researchers, in collaboration with Drexel University, have created a new compound that can be used to 3D print telecommunication antennas and other connectivity devices.
These 3D printed products, created by combining a two-dimensional compound called MXenes with a polymer, can be used as an alternative for metallic counterparts and can make a vast improvement in communication technology including elements such as antennas, waveguides and filters.
Waveguides are everywhere, yet most people don’t know what they are, says Dr. Mohammad Zarifi, a researcher in UBC Okanagan’s Microelectronics and Gigahertz Applications (OMEGA) Lab.
Waveguides are structures or pipes that help direct sound and optical waves in communication devices and consumer appliances like microwaves. Waveguides vary in size, but historically they are made of metal due to their conductive attributes.
Dr. Zarifi and his OMEGA team develop state-of-the-art communication components that have a compatible performance to metal, but are 10 to 20 times lighter, less expensive and easy to build.
“In the ever-evolving landscape of technology, waveguides—a foundation in devices we use daily—are undergoing a transformative shift,” explains Dr. Zarifi, an Associate Professor with the School of Engineering. “From the familiar hum of microwave ovens to the vast reach of satellite communication, these integral components have traditionally been made from metals like silver, brass and copper.”
MXenes are an emerging family of two-dimensional materials—with the titanium carbide MXene being a leader in terms of electrical conductivity, explains Dr. Yury Gogotsi, Director of the A.J. Drexel Nanomaterials Institute at Drexel University in Philadelphia
“Think of MXenes as nanometre-thin conductive flakes that can be dispersed in water-like clay,” Dr. Gogotsi says “This is a material that can be applied from dispersion in pure water with no additives to almost any surface. After drying in air, it can make polymer surfaces conductive. It’s like metallization at room temperature, without melting or evaporating a metal, without vacuum or temperature.”
Integration of MXenes onto 3D-printed nylon-based parts allows a channel-like structure to become more efficient in guiding microwaves to frequency bands. This capability in a lightweight, additively manufactured component can impact the design and manufacturing of electronic communication devices in the aerospace and satellite industry, explains Omid Niksan, a UBCO School of Engineering doctoral student and first author of the article.
“Whether in space-based communication devices or medical imaging equipment like MRI machines, these lightweight MXene-coated polymeric structures have the potential to replace traditional manufacturing methods such as metal machining for creating channel structures,” he adds.
The researchers have a provisional patent on the polymer-based MXene-coated communication components. And Dr. Zarifi notes the potential of this equipment is sky-high.
“While there is still additional research to be done, we’re excited about the potential of this innovative material.,” says Dr. Zafiri. “We aim to explore and develop the possibilities of 3D printed antennas and communication devices in space. By reducing payloads of shuttle transporters, it gives engineers more options.”
The research was conducted in collaboration with scientists from Drexel University’s A.J. Drexel Nanomaterials Institute and supported by the Department of National Defence, the Natural Sciences and Engineering Research Council and the United States National Science Foundation. It was published in the latest edition of the journal Materials Today.
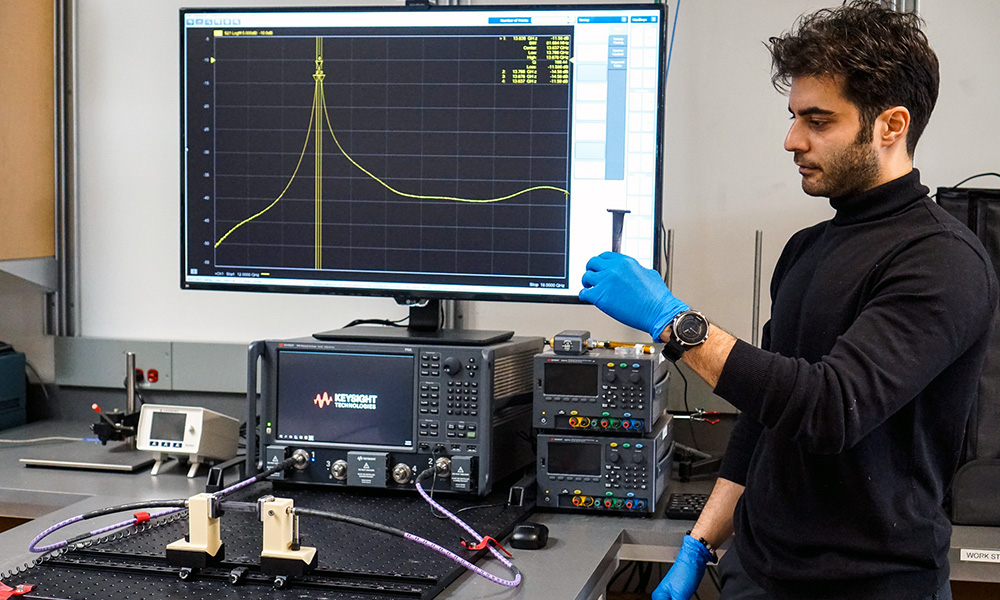
Omid Niksan holds a prototype of a 3D-printed MXene-coated component that can be used as an alternative for metallic components in antennas, waveguides and filters.